5 Best Practices To Follow for Efficient Inventory Management System
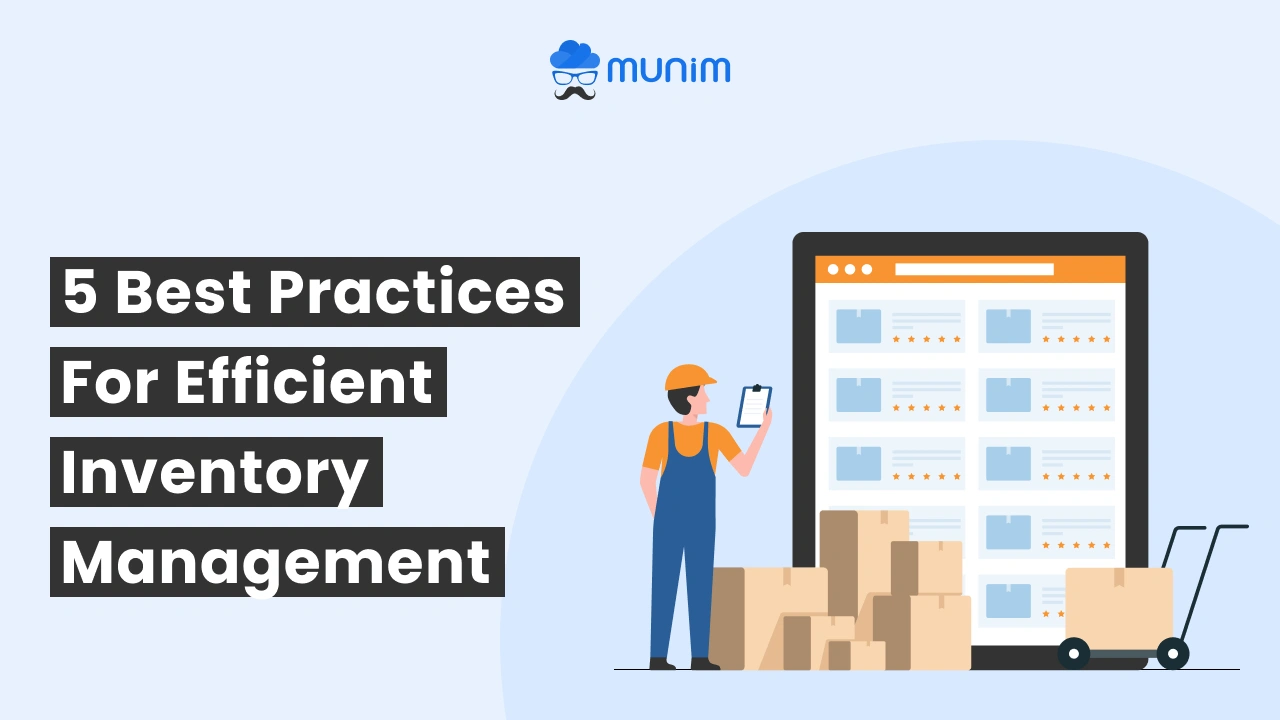
There are multiple factors contributing to the business success and inventory management system falls under the same bracket. Efficient warehouse operations cater to customer satisfaction, profitability, and operational efficiency. Improved inventory control is the secret to customer retention and loyalty. It helps you cater to customer requirements and avoid situations like stock-outs. Also, it swiftly meets sudden spikes in customer needs due to seasonal discounts and festive sales. You can gain a competitive edge in the market with appropriate inventory management.
Proper warehouse operations need inventory management best practices. Here’s a list, checkout now!
5 Best Practices for Efficient Inventory Management System
1. Understand and Segment Your Inventory
Understand, categorize, and manage inventory based on their importance and type. Checkout what are the segments of stocks you handle. See when they are in demand. What do the customers like about the products, and what are their needs? Analyze historical data to identify customer buying patterns and market trends. All these queries will lead you to a better understanding of your warehouse operations.
Categorizing inventory based on importance and movement will assist you in optimizing stock control and focusing on stocks in demand. Here’s how you can segment and manage inventory:
- Segmentation Based on Importance:
- High-value, Low-Sales Products: Monitor these products closely as they are expensive to hold but share significant contributions in revenue.
- Mid-range products with moderate sale: These inventory items don’t need intense monitoring and should be given periodic attention.
- Low-Value, High-Sales Products: These items are restocked frequently as they are in demand and inexpensive. They don’t need much attention and can be managed easily.
- Revenue and Demand-Based Categorization:
Categorize your inventory based on their demand. Monitor revenue-generating items. This will assist you in discovering inventory in demand. Restock frequently purchased items regularly and items not in demand less often. Sales and discounts on products in-stock for a long time will help you free out inventory space. Prioritizing restocking of fast-moving items will help you avoid stockouts, while giving low priority to lingered products will prevent overstocks.
- Festive or Seasonal Segments
Certain products or items are in demand during specific seasons. One of the inventory management best practices includes identifying and segmenting stocks based on seasonal demands. Segmenting stocks based on demand for a particular period helps reduce waste. It also ensures that you don’t run out of stock for high-performing items.
2. Leverage Inventory Management Software
For SMEs, managing inventory is a query of concern. Monitoring and controlling inventory manually is prone to errors and delays. This results in customer dissatisfaction and warehouse issues. An inventory management system delivers real-time visibility into stock levels, preventing stockout or overstock.
The warehouse management software automates monitoring, inventory alerts, and restocking schedules for businesses. This helps them effortlessly track stock levels and restock items before they run out of stock. It automatically notifies about the purchase orders when the inventory falls below the threshold level.
The inventory management software promotes enhanced decision-making through detailed analysis and insights. These reports assist businesses in forecasting future demands, identifying trends, and optimizing inventory more accurately.
If you’re looking for an effective inventory management solution, Munim Accounting and Billing is the best choice! Don’t scroll away; try it now!!
3. Implement Just-in-Time (JIT) Inventory
Just-in-time (JIT) warehouse optimizing strategy focuses on reducing wastage, minimizing storage costs, and optimal resource usage. JIT minimizes the holding costs of stocks by allowing businesses to order products only when they are needed. This lowers unnecessary expenses and operating costs.
For perishable items like food products, it ensures the stock is refilled fresh and consumed before its expiry, eliminating business losses. Also, for fast-paced industries where market trends change continuously, the strategy ensures businesses don’t hold on to outdated trends.
Also, JIT is the best inventory management system that facilitates you to align with the market fluctuations. It allows you to stock up your inventory in response to real-time market demands.
4. Build Strong Relationships with Suppliers
Strategies and software will help you manage your inventory levels. However, ensuring strong and positive bonds with your suppliers will help you achieve your inventory goals. Collaborating with suppliers at different inventory stages will ensure timely deliveries and the best deals.
Healthy communication with the suppliers regarding stock levels, inventory operations, etc., will streamline your supply chain operations. It will also enhance the process through faster reordering, flexible payment terms, and priority access to your business needs.
Strong relations with suppliers will guide you through some of the insights for inventory management best practices. You will get access to market trends, supply chain issues, custom solutions, and customer buying patterns to improve warehouse operations.
5. Conduct Consistent Audits
Regular audits, maintenance checks, inspections, and accurate evaluations are the keys to the best inventory management system. The audit reports and maintenance activities will help you identify whether your inventory aligns with customer demands.
Automated tools for tracking inventory operations are also a better way to stay in line with warehouse standards. Auditing and maintenance activities bring credibility and reliability to your warehouse. They not only help forecast sales but also minimize stock-related issues.
Read More: 5 Inventory Invoicing Software You Need to Check
Wrap Up!
You have understood the best ways to manage inventory efficiently. If you have any further queries, do contact us. We will surely answer them.
Looking for the best inventory management system that fits your business requirements? You are at the right place! Munim accounting and billing offers you the best warehouse management feature! Sign up now!
FAQs
- What are the stages of inventory management?
Scroll down to the list of 5 stages in an inventory management system.
- Raw Materials
- Work-in-progress
- Finished Goods
- Maintenance, Repair, and Operations
- Packing Materials
- What is EOQ?
EOQ stands for economic order quantity. It refers to the ideal amount of units a business should order to meet customer/ market demands. This plays a vital role in minimizing inventory expenses.
- What is MOQ?
Minimum Order Quantity (MOQ) refers to the minimum amount of items sold by a vendor to a customer in a single order. Vendors use this strategy to ensure profits in every order.
- Can I get a demo for Munim accounting and billing?
Yes, you can schedule an online demo with our Munim accounting and billing experts.